Packaging, warehouse operations, and shipping systems are probably not your favorite part of your business, but handled poorly, they can be your demise. Here are the most common packaging mistakes we see manufacturers make:
Favoring Design over Practicality
The consumer might buy your product because of your flashy packaging, but if the product is damaged during shipping because of flimsy or inadequate packaging, it will cause you all kinds of headaches. Your package design should protect your product from environmental damage.
It’s also important to choose a material for packaging that is lightweight enough to reduce your load in the warehouse and your shipping and delivery costs. A heavier package means a bulkier package, which can lead to more strain on warehouse equipment and dropped products.
Favoring Protection over Promotion
There is, however, an important balance between practical and pretty. Like it or not, consumers judge books by their covers. When designing your product packaging, keep in mind that there are two types of packaging: internal packaging and external packaging. Your internal packaging will showcase your product on the shelves for consumers to see. It needs to be marketing driven while protecting the product it holds inside.
External packaging, on the other hand, is all about function and utility. Its primary purposes are to contain the internally packaged products, protect them from damage, and ensure they arrive at the proper destinations. This means making sure your external packaging is sturdy, easy to move, and labeled adequately. When you design your product packaging with shipping in mind, it’s possible to find ways to be more efficient, like using pallets for warehouse storage.
Ignoring the Cries of Tree-Huggers
The movement toward more sustainable packaging is not going away. According to the EPA, containers and packaging alone account for nearly
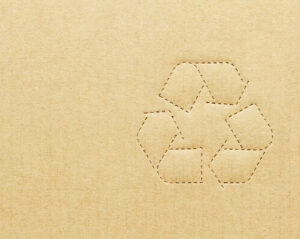
one quarter of the material reaching landfills in the U.S. Many consumers make their buying decisions based on whether the material the product comes in is recyclable. It’s a marketing decision as well as the common sense, responsible approach to packaging.
Use lightweight materials (like recyclable plastics and paperboard) to reduce shipping costs and reduce waste going into landfills. Corrugated cardboard packaging is also extremely lightweight, versatile, sturdy, and easy to recycle. It’s also easy to customize so your external packaging is appropriately labeled for warehouse management.
As an Atlantic Packaging partner, Skybox Packaging supplies 100% recycled corrugated packaging and provides a cost-effective and reliable option for eco-conscious customers.
Poorly Labeled External Packaging
You’ve got your beautiful internal packaging tucked neatly within your external packaging, but now there’s a problem. The boxes are blank. The labels are buried on the inside of the packaging. No one knows for sure which product is in which box.
Poorly labeled external packaging creates confusion and disarray in the warehouse. Mis-picks and mis-packs are an operational profit drain that originates in the warehouse, causing damage to both your physical product and your brand’s reputation. These errors cost you in lost products and lost customers.
Make sure your external packaging has clearly identifiable print & barcode labels. Once that is taken care of, you’ll need to make sure your operations staff understand the process they need to follow to ensure the right products get to the right place, both in your warehouse and when they’re ready to ship.
One of the best ways to do this is to establish a system that rewards employee compliance, accuracy, and productivity. This incentivization helps keep your inventory records accurate. Without lost or mis-picked products, your company will gain an increase in profits. The best place to tighten up profit leaks is by identifying mis-picks.
At Skybox, packaging and warehouse operations isn’t just part of our business—it is our business. We specialize in designing packaging solutions that work, from design to delivery, ironing out and helping to maintain the operational system. Learn more about our services and how we can work to avoid these common packaging mistakes together.